Category: เครื่องแยกและผลิตก๊าซ CO2 & CO2 Recovery Plant > Production - Direct Fired > |
Carbon Dioxide Production (Direct Fired) 
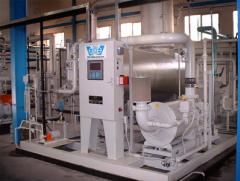
Under some circumstances and in certain areas of the world there is an insufficient supply of high quality CO2 to meet the needs of the market. In the early 1960’s the Wittemann Company responded to this need by developing a line of reliable and efficient flue gas extraction and direct fired CO2 production systems. These systems are employed on most continents of the world, primarily to meet the CO2 demands of the soft drink industry.
Wittemann understands the need for CO2 equipment to meet and exceed the latest CO2 quality specifications. Wittemann CO2 Production Systems are designed to perform by providing proven purification techniques that minimize nitrogen and oxygen in the final product and eliminate NO,NO2 and other harmful impurities. The result is up to 99.99% pure CO2 guaranteed to meet product specifications.
Fuel Oil or Natural Gas Direct fired systems are self contained systems designed to produce a flue gas specifically for CO2 production. Robust component selections and an extensive use of Stainless Steel throughout the solvent system and anywhere saturated CO2 is present ensures a long, trouble-free life.
Key Features
- The Wittemann Stripper Tower is an integral part of the reboiler maximizing availability of solvent steam for stripping duty, promoting complete stripping of CO2 from rich MEA steam and avoiding additional stripping action in the reboiler - a condition which promotes corrosion.
- The Wittemann Absorber Tower with counter current MEA flow improves CO2 absorption and promotes fuel-savings and cost effective CO2 production.
- Wittemann designs and manufactures its reboiler specifically for MEA service. Our two-pass, dry-back design allows operation at near stochiometric combustion - most important when trying to combat the potentially corrosive effects of MEA in the presence of oxygen.
- Extensive low pressure purification yields high purity CO2 as well as extending the life of downstream mechanical equipment by protecting it from entrained impurities and sludge.
- The system employs three (3) stainless steel vessels -- two (2) large diameter, bubbler-type KMnO4 Scrubbers (this makes more KMnO4 solution available for impurity removal and minimizes the frequency of change-out) followed by a third vessel that combines a carbon bed support with a special purifying medium, WittFill, to remove the various products of combustion and compounds formed during MEA degradation.
Complete Control
To put all this technology at your fingertips, Wittemann systems are controlled by a sophisticated, yet simple to configure and operate central control system. At the heart of the system is a microprocessor (or optional PLC controller) that receives critical operating data, then outputs control information to the plant for optimal performance and efficiency. Supplied software provides important features, such as data logging, reports, graph plotting and equipment runtime tracking. The system is designed with flexibility in mind and can be connected to a local computer or remotely connected via modem.